Updates on “5 Questions About Fiber Optic Bonding, Grounding, and Locating”
From the September 2016 OSP Expert Column
Our September 2016 OSP Expert column on fiber optic cable bonding and grounding, co-written by Vernon May and me (mostly Vernon’s work), caused quite a stir. The responses to the 5 questions have ranged from "finally, somebody asked these questions" to "you guys are going to get somebody killed". (You can read this column again at https://isemag.com/2016/09/5-questions-about-fiber-optic-bonding-grounding-and-locating/.)
Given the responses, Vernon offered to address this topic again. Here are his thoughts.
September 2016 Column Summary
Don and I received a question from a reader early in 2016. His position was that he completely understood the company specifications and practices toward bonding and grounding fiber optic cable. They match the copper cable. What he found hard to understand is why copper and fiber optic cable should be treated the same. Don and I looked at the question and could not find a logical reason based on real world conditions.
(Don and I both preach electrical safety, and we both firmly believe that everybody should be following company safety practices without exception.)
Question #1. If we had never worked with copper cable, how much bonding and grounding would we design into our fiber optic network? and Question #5. What about the optical to electrical interface points?
Mr. McCarty:
I am Mike Parker; I am a retired splicing technician from Bell Atlantic (32 years, lineman, frame hop, Installer, repairman, cable and cable maintenance) with 6 years’ experience OSP engineering/Project Managing as a DOD contractor.
I always look forward to my new ISE magazine and the first article I read is yours. I am writing you about the article in the Sept. 2016 issue about grounding the metal parts of fiber optic cables. It was very enlightening and made a lot of sense from an equipment protection view, but I have one observation/question: no mention was made of technician safety.
In the old Bell System, we were always trained that bonding and grounding was supposed to protect the technician as well as the plant. As a cable maintenance technician. I remember running many troubles on cables where the power and telephone cables were damaged during construction, especially directional boring. Many times, the AC would bleed over to the telephone from the damaged power. Since our cables were bonded on both ends we were basically protected from high voltages. I remember removing grounds to locate cable and having the AC arc at which time I would call the power company if it tested as AC and not inducted power. It would seem to me if the metal parts of the fiber cables were open on both ends they would just become a large capacitor and would discharge when the tech became the pathway to ground. Could you comment on my concern? I do some consulting, but don’t work full time anymore, but my heart is always with OSP. Thank you for your informative articles and keep them coming.
Mike Parker
PARKCON LLC
Dear Mike,
Thank you for the kind words and for taking the time to respond. Many readers missed the two direct safety references in the September column. From a purely pragmatic point of view, if we get our readers shocked, we lose readers.
Seriously, technician safety is our top priority. We simply are struggling to find proof that grounding the metals in fiber optic cables improves safety. You could argue that a ground causes a safety hazard in certain situations.
Question #5 has a very simple answer. There is no doubt that in a joint electrical and optics site, national electric standards apply and traditional bonding grounding practices make complete sense.
The ambiguity is focused on optical only sites. First, let’s separate locate wires from armor (not sheath) in fiber optic cables.
Locate wires are designed exactly for their name. They are there as a path for cable locator tones. They are not there to provide safety. These wires can carry about the same current as 19 gauge twisted copper. We get that the wire must be grounded at the far end to complete a cable locate. However, we are on the record stating that the grounds should only be in place during a cable locate and then removed again. Potentially, the locate wire could draw a lightning shot, but it certainly won’t carry the charge. This can cause a physical blow out that can and does damage the optics that would otherwise be isolated from lightning damage, if the wire is floated.
Armor is just that. It is physical protection for the glass inside. Sheath in copper cable is designed to carry induced voltage to ground before it impacts the cable pairs inside. The steel armor will certainly carry more current than a locate wire, but it still does not react like sheath in a copper cable.
Your concern about the "capacitor" effect on unterminated metal along a power path is valid and was cited by another reader (below) and I comment further. Don’s take is that safety practices call for using a hazardous voltage tester every time, so that potential would be flagged with a red light. Hazardous Voltage protocol is well established and should then be followed. Basically, put on you rubber gloves and discharge the potential to ground. The red light will go away. Technicians that do not have a hazardous voltage test tester and certified rubber gloves should see their boss immediately.
Question #3. Assuming that the NESC does not apply, is there a voltage hazard at non-electric sites that requires protection?
Cited: Telcordia SR 1421 20.2.5 Bonding and Grounding of Buried Fiber Optic Cable
• Fiber optic cables having metallic components, including metallic shields, are susceptible to inductive pickup from unbalanced currents in nearby aerial or underground power lines.
If of sufficient length, significant voltages can be induced on the shields. This is the key assumption.
First, I agree with Don on following the hazardous voltage protocol.
The capacitor effect that all of us have seen (and most of us have felt) in copper cables is contributed to by the grounded tips in the cable core. That cable core provides a ground to promote the induction to the sheath around it. Fiber optics should not have that effect.
• Appropriate grounding intervals will reduce voltages to a safe level if a cable were cut or intentionally opened by a craftsperson for reconfiguration or maintenance.
This is certainly true in copper cables. However, they are meant to be bonded and grounded. So, the sheath will be grounded somewhere. If no metal is grounded in the fiber optic, is there any voltage to protect from?
• For various reasons, shields must not be floated. The discontinuities in the shield can result in lightning-related arcs occurring within components and the low impedance to ground will not be high enough to limit current to acceptable values.
This practice is commonly being ignored around power sub-stations. Bonds are floated to reduce the return power voltage on the telecom sheath. And if the armor/wire is not grounded, there is nothing to draw the lightning.
• Fiber cables constructed with double metallic shields must always be bonded together at discrete intervals. In long lengths of cable, significant voltages between two un-bonded shields can develop.
The inner and outer armors probably should be and can be bonded. This can be accomplished without grounding.
• Grounds must be installed at all splice and regenerator locations. It is recommended that power company multi grounded neutrals be avoided as a ground point. While this provides a low impedance ground, it also permits high fault currents to enter the communications plant. In some cases, these currents can overheat and damage optical cable. Since these long-haul fiber cables can run for many miles with no splice or regenerator, there is a possible risk of introducing a power fault through a MGN connection that may travel a long way along the cable and cause damage.
In many ways, this section supports our concerns. Grounds can be the source of problems. Regenerator locations have electrical components and therefore, the NESC and NEC apply. At splices, if fiber optics cable can’t be bonded to MNG, that means we must depend on ground rods. There are several regions where getting a good ground from a ground rod is very difficult. Try driving an 8-foot ground rod into granite. Too often, they go 3 feet down and are cut off with a hacksaw. How much protection is really being achieved?
INDUSTRY RESPONSE to the September Column
A major hardware vendor was interviewed. Their position has been echoed since by other vendors. Basically, they have no position beyond following the specifications of their customers. They understand the specs very well and meet them. Questioning customer specifications is not considered to be part of their scope.
Independent service providers have flexibilities that are not available to the larger providers. For example, having a spec and practice fit all conditions in one county is easy when compared to trying to cover an entire region. They generally do what makes sense for them, so there has been some adjustments made in the fiber optic bonding and grounding practices in some areas since the article was released.
As we hoped, at least one major service provider examined their practices on bonding and grounding fiber optic cable since the column was published. The report back was not surprising. Though, many of the practices could not be independently and/or directly justified, the perceived potential safety issues prevented any policy changes.
OUR ANSWERS
Question #1. If we had never worked with copper cable, how much bonding and grounding would we design into our fiber optic network?
This was the primary question. It is obvious that fiber optic bonding and grounding practices are rooted in the copper cable bonding habits. It appears that at least some overkill is being practiced daily.
Question #2. Is the NESC applicable to sites where there is no electricity flowing?
If the NESC or NEC is read in detail following application references, direct application of either one to fiber optics appears to be an assumption based on tradition. Telcordia SR 1421 20.2.5 does directly apply, but it also raises some significant questions.
Question #3. Assuming that the NESC does not apply, is there a voltage hazard at non-electric sites that requires protection?
The only commonly cited potential danger was induced voltage from power lines. As stated before, we believe that copper will induce more voltage due to the tip side grounds in the core. The theory that ungrounded metal in fiber optics will induce hazardous voltage should at least be quantified, if not more completely qualified.
Question #4. Why do we have metals in fiber optic cables, if we should not ground them?
Armor is armor and locate wire is locate wire. Neither are in place for technician or plant electrical safety.
Question #5. What about the optical to electrical interface points?
Electrical equipment onsite automatically puts both the NEC and NESC into force.
Signing Off
We really appreciate the feedback and discussion on this subject. We knew it would be impossible to put this issue to rest in our column, but we believe that we have generated a meaningful discussion on an important matter. We hope for further investigation by entities that have access to the equipment required to be thorough. Fire up that Tesla coil. Please, help us to continue to contribute by sending in your questions and best practices. You can call me at 831.818.3930 or email [email protected].
About the Author
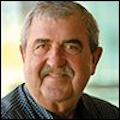