Behind the Invisible Networks
6 Steps to Build a Subsea Cable System:
Talking on a cell phone or sending an email, we can easily forget that 99% of the world’s Internet traffic takes place under the sea. Along the ocean floor runs an invisible network of optical fiber cables delivering the magic behind data traversing continents and the everyday reality of instantaneous communication between people and machines thousands of kilometers apart.
Ever wondered how the arteries of the Internet’s circulatory system are put in place? We have a unique vantage point given that we’ve co-developed, and now co-manage, a very important undersea optical fiber network connecting Africa to the Internet: the West Africa Cable System spanning 17,916 km from South Africa to the UK, connecting 10 African countries. We are also constructing the South Atlantic Cable System, covering 6,500 km between Africa and Brazil, and the Monet Cable System, running more than 10,500 km between Brazil and the US.
To simplify things, below are 6 steps to build a subsea cable system:
Step 1: Desktop Research
Existing information is compiled and analyzed to identify a feasible undersea route and the cable landing station positions along the route where the cable will be connected when it emerges from the sea. Preliminary engineering plans are then drawn up that are used for the planning of the actual undersea survey
programs prior to field survey mobilization.
Step 2: Field Survey (Sea Bottom and Planned Route Study)
This is one of the key steps before the underwater technology (consisting mainly of special undersea cables and optical amplifiers) can be engineered. As this cable will be laid on the seabed it is important to first form a "picture" of the seabed, including its composition (i.e., rock, sand, or soft sediment) and to identify any large obstacles such as wrecks and ocean canyons which cannot be seen in deep water from the surface. To do this, survey ships equipped with Side Scan Sonar, Multi-Beam Echo Sounder, Bottom Profiler, and a Magnetometer, are used to perform deep water and shallow water surveys as well as a burial assessment study. The end result is a Route Position List (RPL) and a Straight-Line Diagram (SLD) which is used to determine the shortest and safest route to lay the cable along, as well as the type of cable protection to use for the identified route.
Step 3: Equipment Procurement
The submarine cable, optical repeaters, and equipment that will provide electrical power to them are referred to as the wet plant. Once the route engineering process is concluded, the engineering process of the equipment that will enable optical transmission over this cable can start; this equipment is referred to as the dry plant and will eventually become the point at which other networks can connect in the future to enable connections to the Internet.
Once concluded, the procurement process can start with the selected supplier to implement the system. This is usually done on a turnkey basis whereby the supplier is responsible for the total delivery of the system as agreed. The owners, however, take full responsibility for the readiness of the cable landing stations.
Step 4: Manufacturing and Installation
The wet plant is manufactured in specialized cable manufacturing facilities and loaded onto the cable installation vessels specifically equipped for the task, as per the engineered route. Depending on the size of the network, installation often takes place in concert with the manufacturing to save time. The dry plant equipment is manufactured and tested in the precise configuration as it will be installed in each cable landing station before being shipped for installation.
Step 5: Training and Testing
Various electrical, optical, and mechanical tests are performed to ensure the system is properly installed and is fully operational. In addition, training is provided on safely operating, monitoring, and maintaining the system so that it lasts for at least 25 years.
Step 6: System Acceptance
Following manufacturing and installation, the system is accepted in various stages. However, when all major identified issues have been cleared, and staff have been trained to operate and maintain the system, it is ready to carry Internet traffic.
About the Author
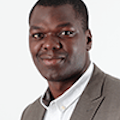