Heat and Batteries Don’t Mix:
The rising demand for instantaneous data has placed unique burdens on network suppliers, requiring the addition of more equipment into data centers and central offices. This equipment generates additional heat, necessitating lower set points for air conditioning. The end results are higher energy costs and higher Total Cost of Ownership (TCO) of the batteries.
The average piece of industrial electronic equipment, including those implemented in telecom applications, is specified to operate at an ambient temperature of minus 40°F (-40°C) up to 140°F (60°C). Operating equipment at temperatures above this range can cause premature failure of the equipment. For every 50°F rise in temperature of electronic equipment, there will be a 50% loss in its reliability.1 Traditional lead acid batteries perform best at ambient temperatures of approximately 77°F (25°C). For roughly every 15°F (10°C) rise above 77°F (25°C), the float life of a Valve Regulated Lead Acid (VRLA) battery is cut in half.2 This is offset by the fact that on average, a 1-second power outage costs a business $1,477, creating a need to find a battery that will handle the higher heat of today’s systems to keep them working.
The main ingredient of traditional batteries is lead. In its purest form, lead is a difficult material to work with as it bends and stretches very easily. To improve its workability, other metals, such as antimony and calcium, are added to the mix, stiffening the grid and helping to make the grid easier to handle during the manufacturing process. A standard lead calcium battery is made of both positive and negative grids that have a paste of lead oxide (positive) and sponge lead (negative) coating them. This paste reacts with a solution of sulfuric acid to create a chemical reaction, electricity that is bussed to the terminal block.
These additives have an impact on the functionality of the battery. Heat drives chemical reactions in lead acid batteries. Elements that corrode in sulfuric acid will corrode more quickly in a high-temperature environment. The addition of calcium to a lead acid battery causes the battery to corrode almost immediately when exposed to the sulfuric acid within the electrolyte. The result is more frequent battery replacements as well as an increase in TCO.
To counter premature battery life failure, products utilizing Thin Plate Pure Lead (TPPL) technology have been employed. These feature 99.9% pure lead grids and paste and are subjected to extremely tight specification and process controls. All of which minimize the common corroding elements. This lack of corrosion allows the grid to remain intact and creates minimal venting, which extends service life even at high temperatures.
As was previously mentioned, lead in its pure state can easily be bent and stretched. This factor has made the process of creating a pure lead grid difficult. It wasn’t until the mid-1970s when the Gates Corporation introduced a new generation of lead acid batteries, known as VRLA, which utilized a closed system design. The electrolyte in the VRLA battery is captured in an Absorbed Glass Mat (AGM) that is compressed, providing even contact across the entire plate and ensuring consistent power. The design creates a recombination environment, which returns water to the battery, reduces maintenance, and prevents dry out.
The Gates Corporation’s VRLA battery was ahead of its time. A pure lead battery, it featured a spiral-wound cell with very thin, pure lead electrodes contained under high compression. These early pure lead batteries offered high density at the cell level, and extremely long life with little maintenance compared to the traditional flooded battery. Unfortunately, the space savings achieved from the energy-dense, cylindrical cells were greatly diminished when 2 or more cells were combined into 1 battery (usually 6 cells to generate 12 volts) due to the voids between the cylinders.
It wasn’t until the early 1990s that manufacturing methods evolved to create what is today’s flat plate technology. These larger-format, flat plate TPPL batteries were ideal for supporting data centers, wireline and wireless outside plants, as well as remote cabinets, cell site interface cabinets, and Directional Antenna Systems (DAS). Through evolution of the manufacturing processes, larger and larger form factors were created to yield TPPL batteries as small as ½ Ampere hour (Ah) up to more than 900 Ahs.
Combining the years of experience and knowledge with advanced equipment is part of a delicate balance with the materials to make the product perform better than traditional lead calcium products. Any uncontrolled, untested deviation can result in premature battery failure. The key to success is rigid control of all aspects of this operation.
3 Requirements
In terms of the next evolution of battery technology, there is more to address than just the grid to ensure that the full benefit of battery chemistry can be used to its fullest. Heat takes its toll not only on accelerating corrosion but also on the plastic used to manufacture the jar or envelope encasing the cells. Higher temperatures result in the plastic material softening and bulging. This softening leads to reduction in compression, causing higher resistance and more heat.
Since compression is a major factor in ensuring that there is even and consistent contact between the saturated AGM and the grid, a unique engineered plastic resin is needed that includes polycarbonate to ensure that the required stiffness to keep compression at high temperatures was maintained. Bunsen valves used in TPPL batteries also need to be designed to operate continuously at high temperatures over the life of the product, while also appropriately interacting with the lid in which it is assembled.
Today’s batteries demand an extended shelf life. Those with a low corrosion rater allow this with minimum voltage degradation. Some batteries may use catalysts that can reduce float currents and the corrosion associated with them. But those with calcium will still corrode, which limits service life and especially shelf life.
Engineers today are looking for a battery that can withstand continuous temperatures of 95°F (35°C) and spikes as high as 149°F (65°C).
Three factors they should look for in a next-generation battery are listed here.
1. High-Temperature Plastic
One of the key items of concern is the plastic used to make the battery jar. VRLA batteries, and in particular TPPL batteries, require the jar to provide compression between thin plates and AGM material so they remain in constant contact. The plastic also needs to meet certain flame retardant criteria. As a rule, as the temperature rises, batteries housed in the current plastic used begin to soften and bulge. This leads to a loss of compression between the plates and the AGM material. Lack of compression results in increased resistance, generation of additional unwanted heat, and the potential for a thermal runaway. As a result, engineers need to find a plastic that has a high heat tolerance and does not bulge. It is also important that it is easily molded.
2. Rapid Plate Growth
Higher temperatures create an increase in the speed of corrosion and plate growth, both normal processes in a healthy battery. However, this accelerated growth needs somewhere to go, or shorts are experienced. As a result, there is the need to find additional room in the jar to accommodate this plate growth. Creating a larger jar is not an option, as accepted form factors used by customers must be kept for the batteries to fit in existing racks and cabinets. One such product that meets this demand is a 190 Ah form factor in our solution. It is rated at 170 Ah. (See Figure 1.) This allows room for the plates to grow unencumbered and continue to function as designed.
Figure 1. PowerSafe® SBS XL batteries product portfolio
3. Electrolyte Saturation
The ideal high temperature battery is designed as a continuous float application, and the electrolyte saturation for this product is critical to ensure that the battery does not experience dry out. In addition, cold-rolled positive plates are needed to ensure that the granular structure is smooth and compressed as much as possible.
As telecom applications continue to increase in complexity, new battery advances for data centers and central offices can now battle their Enemy Number 1 by raising the set points of a facility’s air conditioning and reducing the replacement and maintenance costs of batteries over 10 years.
Endnotes
1. Patterson, Michael K., "The effect of data center temperature on energy efficiency" In Proc. of ITHERM, May 2008, p. 1173 (p. 7 of PDF), https://pdfs.semanticscholar.org/668c/d2b3e21ae13faf2d7a269054512863fe995e.pdf
2. Air Force Pamphlet 32-1186, "Valve-regulated lead-acid batteries for stationary applications," By order of the Secretary of the Air Force, Aug. 1, 1999, p. 49, http://static.e-publishing.af.mil/production/1/af_a4_7/publication/afpam32-1186/afpam32-1186.pdf
Save
Save
About the Author
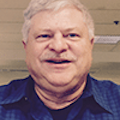