Underground Conductor Locating
Pity the poor cable locating tech. This is the type of job that requires great skill and dedication, and more than just a little luck. It is also a job that can produce terror and prayer. All this is compounded by cable maps without proper footage, not drawn to scale, and outdated by 2 or more years of change. Yet, the locator is expected to be 100% accurate in the task. A cable cut is an instant judgement of the accuracy of the location. No excuses are acceptable, and no quarter is given. You cost us money; you go home and think about it for a while.
Cable locators are judged by the number of cuts they make in a given period of time. Some are luckier than others. If the contractor doesn’t dig where the locator missed, nobody knows, including the locator himself.
The average full-time cable locator mislocates some 10% to 20% of his locates daily. This is not to say that the locator mislocates a section of cable for its entire 325 feet. We are saying that in that 325 feet, he misses a slack loop, buttsplice, or unmapped lateral — that’s a mislocate. If the contractor doesn’t hit one of these anomalies, everyone’s home free. When he does, it’s soap opera time.
When a cable is damaged, it’s usually a big one, or a fiber cable. A big cable or a fiber cable out of service produces great financial loss and management ire. Management sends the man home for a day or two to think about it. And then puts him back in the field with the same test sets and skills. Advice: if you have a discipline problem, send the tech home. If you have an educational problem, train the tech.
There are currently more than 23 major brands of cable-locating test sets utilized to find the path and depth of underground conductors. Despite this variety, there is no one brand that will do every job completely; and, for some 10% of underground conductor configurations, there is no electronic device that can pinpoint them precisely. Knowing this can lead to sleepless nights, but when a technician is schooled in the plant and what might be out there, a more careful, competent, and skilled location process will greatly reduce cutoffs.
History
Since the first telephone cables were placed underground in 1883, cable locating has been a challenge — and back then, not unlike today, training wasn’t a priority. They did realize however that conductive telephone cables disrupted the natural magnetic flux of the earth, and a pair of wires could be used to find this disruption.
The first test set was a pair of rods: a technician held a rod in each hand, pointed straight ahead, carefully balanced so the slightest change would affect the rods. As the technician worked the area, the rods would swing either in or out, parallel with the cable path, as the cable was crossed. In dry soil, where sensitivity was not good, the more experienced technicians found it more effective to remove their shoes in order to become more conductive and increase wire sensitivity. Keep in mind that the rods will react to anything conductive. Old beer cans, a garbage can lid, or anything metallic, has an effect on the procedure.
As more and more cable was placed underground, and as the sheathing techniques improved, a more reliable location procedure was needed. Early cable sheath was lead, sometimes with a jute-covered-tape armored protection. This made the cable more difficult to damage inadvertently, but it also made it hard to locate because the armor protection absorbed the tone. Technicians were forced to locate the exact position of the cable by digging to expose it — which is not a bad idea still today, whenever there is any doubt on a locate.
Eventually, technicians discovered that an amplifier and exploring coil, held in the proper attitude, would pick up any AC voltage induced into the natural magnetic field of the cables. Not all areas had usable induced AC, however, so a method of inducing tracing tone into the cable was sought.
The Western Electric 20C test set provided the first reliable AC tone source. The tone was derived from the same AC ringing current used by technicians to locate solid resistance faults. This set used a Ford Model T coil and an interrupter to produce a low frequency, 20 cycle-per-second tones with a peak voltage of 900 volts. Four 1.5-volt dry cell batteries powered an identifiable tone as far as 1,500 feet on direct buried, common grounded cables.
The 20C could still provide the most accurate locates on all cables, but the problems caused by the audible tone (the frequency of which was in the range of human hearing), led to its demise. Low frequency tone interfered with subscriber service. Trouble reports listed everything from Martians invading Earth to someone tapping their lines. Cable test centers spent a large amount of time explaining to customers why the tone was on the line.
The breakdown set was also used for cable location. A 93-type receiving coil was used with a 147-type amplifier as an audio receiver. The problem here was that the maximum of 90 volts peak would not carry the tone far enough for effective cable locating.
The need to increase the tracing frequency above the range of human hearing brought about the Fisher M-Scope. This test set soon became the industry standard for cable locating. It used a direct connection hookup, and also had the capability to induce tone into the natural magnetic field of a cable simply by setting the transmitter on the ground. A large open transmitting loop was used to send the tone. This induced high frequency broadcast tone all over the place, which was fine in rural or uncomplicated plant, but a problem in congested plant.
The Fisher M-Scope was not the end of low frequency tracing tone. There were many common grounded lead and tape armor cables that the M-Scope couldn’t locate, and telephone companies had to bite the bullet and use low frequency even though customers complained. Modern low frequency sets use a much lower voltage, which reduces range but affects fewer customers. The simple fact is, no one cable locator on the market can locate all underground telephone cables in all situations in the field today.
Selecting cable locate test sets
Cable locating test sets can be broken down into 2 basic categories. Low-frequency locators, which are clones of the 20C, do the best job for accuracy keeping in mind that it takes time to set up. High-frequency locators, clones of the Fisher M-Scope, can be used for convenience but accuracy is sacrificed.
NOTE: Watch out for buried cable TV. Because the conductors are usually buried quite shallow, they will pull a majority of tone and cause a miss-locate. When such a condition is suspected, use low frequency.
The purchase and use of a locator depends on many factors. The specific task of the operator needs to be discussed. Don’t be fooled by price alone. Many inexpensive (not cheap) locators can outperform the big guns in the right situation. There is no need in a non-congested area to have a locator with all the bells and whistles, because, with no other conductors present in the area, all locators work. So, a technician whose primary use of a locator is repairing buried service wires does not need the more expensive test sets with every feature known to man installed. The savings could well be spent on some form of sheath fault locator to pinpoint conductor and shield faults.
Accurate cable location requires not only a well-trained, well-informed, dedicated technician, but also an informed and cooperative manager who provides proper equipment and training, and who will carefully investigate a damaged cable before arbitrarily placing blame.
In cable defense, choose your weapons well. With the right machine, a good knowledge of your plant and other underground utilities, and understanding how to locate in the first place, the number of damages can be reduced drastically.
Signing off
Thank you, loyal readers! This past month I received several emails and texts about a previous column. It matters to me that I am sharing information that can help you do your job, so if you have anything you want to ask, or have ideas for future columns, please email [email protected].
About the Author
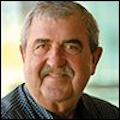