Fiber Sensing Makes Cents for Your Future —
Have you ever wished you could be automatically alerted to any digging near your network? Wouldn’t it be great if you knew the exact location of the digging, so you could go right to the site and protect your assets? Believe it or not, Distributed Fiber Optic Sensing (DFOS) technology can do that, and much more. In this article you will learn more about this powerful technology and some of its applications.
DFOS is similar to standard OTDR measurements in many ways. It can pinpoint "events" with surprising accuracy. Yet, it can do this over fiber lengths of up to 60km. With the right software, it can monitor a fiber continuously, and automatically provide alarms for specific conditions.
But, DFOS also differs from OTDR measurements in important ways. Although optical fiber losses are often caused by external factors, a standard OTDR can only measure the losses — not the factors that cause them. DFOS works the other way around. A DFOS system measures external factors, like temperature, strain, and acoustic vibrations. Basically, the fiber itself is being used as a sensor, which is monitored using special equipment (hence the name "Fiber Optic Sensing"). These factors don’t have to cause losses in order to be measured; and, systems can be built to monitor more than one parameter using a single cable. Figure 1 shows an example in which Temperature measurements were made before and after energizing an electrical power link.1 Temperature measurements were made along the entire length and used to identify hot spots.
Figure 1. Distributed Fiber Optic Sensing of Temperature Along an Electrical Link
The underlying principles of DFOS equipment are complex, and vary with the kind of measurements being made. Some systems rely on backscattered light, similar to an OTDR. Others monitor transmitted light in special ways. Although they may sound exotic, these are mature technologies with simple, user-friendly interfaces. You don’t need to understand the science behind them to put them to work.
It’s important to note that DFOS is distinct from discrete fiber sensing. As the word Distributed suggests, DFOS allows measurements along the entire length of an optical fiber — not just at specific or discrete points. DFOS can also be done with standard optical fibers. Together, these features allow many measurements to be made reliably and economically over long distances.
How Is DFOS Used?
As we saw earlier, DFOS can be used to measure temperature, mechanical strain, and acoustic vibration. This opens up many potential applications. For this article, we are focusing on just a few of the most common ones.
Application #1: Pipelines
Pipelines are the safest way to transport fuels and other hazardous liquids over land.2 Nonetheless, in the last 20 years, there have been 5,679 accidents classified as Serious Incidents, resulting in 310 fatalities, 1,301 injuries, and $7.8B in losses in the US alone.3 (See Figure 2.)
Figure 2.
DFOS provides many ways to prevent incidents or reduce their severity. A fiber optic cable is buried alongside the pipeline and connected to suitable monitoring equipment. Each type of equipment detects problems in different ways.
Distributed Acoustic Sensing (DAS) allows the detection and location of many phenomena by recognizing their acoustic "signatures". Because they’re under pressure, even small pipeline leaks can easily be detected. This allows earlier intervention, before the leak can grow bigger or spill more material. Sudden, catastrophic leaks can be contained more effectively simply by knowing exactly where they are. Unauthorized construction and theft can also be detected using DAS. These activities can be stopped before significant damage has occurred.
Distributed Strain Sensing can be used to detect ground and/or pipeline movement. This is extremely helpful in locations prone to landslides or other ground movement problems, since smaller, harmless movements usually precede major ones. Figure 3 shows a series of strain measurements taken over time with a DTS system. These measurements allowed the pipeline owner to inspect the affected area and take preventive actions before failure occurred.4
Figure 3. Imminent Landslide Detected Via Distributed Fiber Optic Sensing
Distributed Temperature Sensing can also be used to detect leaks. Many materials cause temperature changes in the surrounding soil when leaking out of a pressurized pipeline.
Application #2: Perimeter Security
Foot traffic, vehicle traffic, and various construction activities each create unique acoustic "signatures". These can be automatically interpreted and located using DAS. A fiber optic cable is simply buried along the perimeter, then monitored with DAS equipment.
If you stop to think about it, this is an incredibly powerful tool. Many activities can be hidden from sight by a building, trees, topography, or the cover of darkness. But, it’s extremely difficult to do anything in complete silence. This is made even more challenging by the fact that sound travels so well through the ground.
DAS Perimeter Security can also provide tremendous labor savings. Imagine the manpower required to continuously monitor the perimeter of a large facility. Now imagine a small staff that can focus on intervention without delay or worries that posted monitors have missed something.
Application #3: Incremental Revenue
With all the recent M&A activity, it should be clear that dark fiber is a big business. If you have valuable Right-of-Way with dark fiber, it can produce significant incremental revenue.
For greenfield projects like new pipelines, the incremental cost of adding fiber cable is very low. The cost of adding some extra fiber to that cable is lower still. Even for retrofits, the incremental cost of additional fibers is small compared to the overall project cost. So, even though DFOS may not generate revenue directly, you can improve safety and increase revenue at the same time.
Fiber and Cable Selection
The fiber type used for a DFOS project must be compatible with equipment being deployed. It should also be suited to the type of cable being deployed. Even fibers of the same type can perform differently in DFOS applications. For example, some Standard Single-Mode (G.652.D) fibers work better than others for Temperature and Strain measurements based on the Brillouin scattering method.
So, if you want to leverage this benefit, it’s best to engage both the cable and equipment suppliers up front. Ideally, your cable supplier should have access to a wide range of fibers. This will make it easy to get the best fiber for your application and preferred equipment supplier.
Telecom cables should be designed to minimize fiber strain when the cable is under tension. This helps keep fiber attenuation low and ensure fiber reliability. Incremental dark fiber for telecom applications should be cabled this way.
Strain-free fiber is required for some Distributed Temperature Sensing applications. This will limit cable selection, since not all designs are capable of keeping fibers completely strain-free. Gel-filled, stranded, loose-tube cable is a good option for this application.
On the other hand, Distributed Strain Sensing equipment does not work well with cables that prevent fiber strain. For these applications, fiber strain must closely track cable strain. Yet, fiber attenuation must remain very low, or the system can’t be operated over very long lengths. This is a unique challenge that can be solved by utilizing a solution called Prysmian’s OptiStrain™ modules. Specially selected fibers are placed in a sub-unit that tightly couples the fiber to the cable with as little stress as possible. This keeps fiber attenuation low under normal operating strains, while allowing even very small strains to be reliably detected. Modules can be combined with standard buffer tubes in the same cable core. (See Figure 4.) This allows a single cable to be used for Dark Fiber, Temperature Sensing, and Strain Sensing.
Figure 4. Prysmian DFS™ Pipeline Cable with OptiStrain™ Modules
Conclusion
DFOS is used to monitor Temperature, Acoustic Vibration, and/or Strain, along the entire length of an optical fiber that can be up to 60kms in length. DFOS systems can be used in many applications to automatically identify and precisely locate problems. DFOS installations can also be leveraged for incremental dark fiber revenue.
The ideal fiber and cable type depends on your equipment choices, as well as environmental factors. If you’re considering an installation, be sure to get both your equipment vendor and your cabler involved early on, and explore ways the right underground fiber can serve dual or even triple purposes.
Fiber Optic Sensing Association (FOSA) is a non-profit organization created in Washington DC in 2017 with the mission of educating industry, government, and the public on the benefits of fiber optic sensing. Through webinars, videos, white papers, public presentations, and public policy advocacy, the organization provides information on the use of fiber optic sensing to secure critical facilities, enhance public safety, and protect the environment. If you’d like to learn more about DFOS, check out the FOSA website at www.fiberopticsensing.org.
Endnotes
1. DEH Cable System Preventative Protection with Distributed Temperature and Strain Sensors, F. Ravet, A. Bornes, C. Borda, E. Tjaland, H. Hilde and M. Nikles, Proceedings of the 9th International Pipeline Conference, September 2012.
2. "Safety in the Transportation of Oil and Gas: Pipelines or Rail?", Fraser Institute Research Bulletin, K.P. Green and T. Jackson, August 2015
3. "Pipeline Incident 20 Year Trends", US Department of Transportation Pipeline and Hazardous Materials Safety Administration website, www.phmsa.dot.gov/pipeline/library/data-stats/pipelineincidenttrends.
4. A Decade of Pipeline Geotechnical Monitoring Using Distributed Fiber Optic Monitoring Technology, F. Ravet, E. Rochat and M. Nikles, Proceedings of the ASME 2017 International Pipeline Geotechnical Conference, July 2017.
About the Author
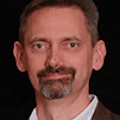