The More They Remain the Same — With Your Batteries —
The equipment and technology that produce the revenue for the majority of the ICT industry is continuously changing by adding more capability and features. There is ongoing effort and investment into the very next version of whatever piece of equipment or technology to keep up with, or offer more than the competition. This is your revenue stream that you need to protect.
However all of this equipment is useless if it ceases to function due to a power failure.
While many sites still use vented lead-acid (VLA) batteries, the majority now use valve-regulated lead-acid (VRLA) ones for a variety of reasons, such as reduced space requirement, no free electrolyte, lower ventilation needs, and reduced maintenance.
Many locations have on-site generators which have the capability to sense when there is a loss of AC power. Or the DC bus drops to a certain value and automatically starts up to provide power until off-site power is restored. That said, no generator starts fast enough and supports your revenue generating equipment in order to maintain uninterrupted operation without a battery that provides the ride-through time required.
Many more sites do not have on-site generators. At these sites the batteries need to support the loads until off-site power is restored or portable power can be brought to the site.
Many locations have unstable power, or no off-site power at all. Often at these sites, a generator is the prime source of power. There also are hybrid sites with various sources of power producing equipment in addition to (or in place of) the generator. These sources can include: wind, solar, fuel cells, something else, or a combination of these. All of these, however, need a battery of some sort to ride through times when that site’s primary power producer is not functioning.
At many of these remote sites the batteries are cycled daily, in that they provide the power to the equipment until they decline to some specific voltage point, then the generator starts and provides power to the rectifiers which recharges the batteries up to a certain level and/or until a specific level of recharge is reached, and then it shuts off and the batteries return to supporting the load — and that process repeats itself over and over.
These applications require batteries that are rugged, dependable, forgiving, and, if possible, field-recoverable.
Industry forecasts show that between 90% and 95% of the standby batteries providing backup for sites that are non Energy Storage Systems (ESS) are lead-acid of either the VLA or VRLA designs (Avicenne Energy Report AVIC2017 and the FINAL-BCI Industrial Battery Forecast 2018-2020).
This is because they are universally available, easily understood by anyone anywhere, manufactured and recyclable globally, simple to install and maintain, reliable, predictable, and do not require a battery management system to function properly and safely. One added benefit is that if something does go severely wrong (e.g., thermal runaway) they are typically less destructive to nearby equipment than some of the more energy dense technologies.
InvisiLight® Solution for Deploying Fiber
April 2, 2022Go to Market Faster. Speed up Network Deployment
April 2, 2022Episode 10: Fiber Optic Closure Specs Explained…
April 1, 2022Food for Thought from Our 2022 ICT Visionaries
April 1, 2022Recycling
Of substantial importance to those that are concerned about our environment and what we will leave to future generations, is that they are recyclable all over the world. Over 99% of a lead-acid battery is recyclable. I mention this because some battery technologies are not presently recyclable. However they are being deployed with the anticipation that they will be re-purposed after they no longer can provide the power needed for their existing application. Re-purposing of lead-acid and Ni-Cad batteries has been performed for many years, as their capability or their application changed, but eventually they are recycled. Re-purposing is not recycling.
Eventually all battery technologies will need to be recycled or disposed of. Let us hope that we do not learn the hard way that any of these technologies ends up not being able to be recycled, but rather ends up being disposed of like our plastic bags (and other single-use plastic items) do. We know that many of these single-use items can end up in some country that is willing to take other’s trash for cash. We also know that in some countries, hazardous, toxic, and dangerous, wastes are left for others to clean up.
The Bestmag Batteries & Energy Storage magazine, No. 63 Winter 2019 issue, has 2 articles: "Recycling Shambles of Europe’s ‘Disappearing Batteries’" and "Industry sounds alarm over lithium battery dumping." These explain that illegal dumping of lithium-ion batteries in with residual waste in Europe is causing fires and destruction, putting workers at the waste sites at risk, and has cost over €100 million (US $113M).
Everyone surely understands that all of that plastic floating in the oceans did not get there by accident, and that most likely much of it was deliberately dumped there. We also need to realize that as long as there is money to be made by illegally disposing of waste that is not recyclable, that there are those who will do that for you, and if it is denser than water then it will sink. Out of sight, out of mind.
Not Your Father’s Battery
The lead-acid batteries produced today are built based upon experiences, research, and technology breakthroughs, in all facets of battery design, materials, and manufacturing. Not all that long ago many lead-acid stationary designs were not designed for repeated cycling, operating in hot environments, or being left in a partial state of charge (PSOC). With many earlier VRLA designs, while most could handle many hundreds (or thousands) of cycles if properly recharged, they were often susceptible to premature capacity loss (PCL) which impacted their ability to perform as expected, and the length of their useful lives.
One cause of PCL with VRLA cells was (and often still is) excessive off gassing, which leads to under saturation (dry-out) of the cells. This can occur under normal float charging (not just when the battery is being overcharged). When this occurs it causes a change of internal resistance, increasing charge current, and continues on at an ever-increasing rate until failure. This reduction in saturation of the cells also reduces the ability of the cells to dissipate internally generated heat to the outside of the cells, which eventually will lead to thermal walkaway and then runaway.
Years ago it was thought that the only solution for PCL caused by dry-out was replacement. However it is now understood that re-saturation can recover many of these failing cells and extend their useful lives. This solution is presently being implemented by various companies around the globe.
At off-grid sites, there is a substantial difference in how many hours a day the generator is required to run in order to recharge the cycling battery depending upon if the battery is properly saturated or not. A properly saturated battery equates to less fuel costs, and less wear and tear on the generator than one that is not.
Like this Article?
Subscribe to ISE magazine and start receiving your FREE monthly copy today!
Preventing Thermal Runaway
Thermal Runaway which was once thought to come without warning, is now better understood and does provide multiple advance warnings before occurring in all instances. With any lead-acid battery you need only 4 battery measurements to alert you to a problem. These measurements take less than 2 minutes to execute. There is a free program, "Thermal Runaway Detection and Prevention Guide", where you fill in just 4 measurements and it informs you of problem-causing issues which can be downloaded at http://www.batteryresearch.com.
Figure 1. BEM installation showing current and cell temperature sensor placement on this design battery.
This can also be accomplished remotely with any simple 4-point monitor such as the one shown in Figure 1. This Battery Event Monitor (BEM) alerts you instantly to changes as they occur, so that you can take action as appropriate. By measuring and trending just the over-all voltage (OAV), current flow with timing (charge or discharge), a cell/unit temperature, and ambient temperature, these can provide you information on a battery entering thermal walkaway (prior to thermal runaway), site battery runtime, HVACs, charger, capacity estimation, and dry-out issues. A lot of information from a small box.
All manufacturers have made improvements to prevent premature dry-out. These include design, materials, and process changes, plus some are installing catalysts in the head space of the cells in order to prevent dry-out and maintain proper saturation. These are particularly beneficial where hotter than standard temperatures are experienced, as dry-out happens more rapidly in that condition. Yes there are smart chargers which will temperature compensate within limits, but a catalyst will provide a benefit if the battery is either on charge or off charge. For the majority of 2-volt cells that have removable vents, there are catalyst equipped vents available which are easily field retrofitted, if they were not provided from the factory. Very often these field catalyst additions are installed at the same time as the IOVR™ process. With cells that do not have removable vents there is now a process that allows both water and catalyst additions, however this needs to be performed by a trained technician.
Internal ohmic readings on VLA or VRLA cells will not provide a capacity result but will inform you of changes internally to the cell/module. With conductance values a higher number is better. Figure 2 shows the before and after conductance values 24 hours apart, on 2 strings that the IOVR+™ process was performed on. These 7-year-old strings were in a climate-controlled environment, but obviously were suffering from dry-out. There was a 35%+ improvement in the average conductance values of these cells from 3,031 to 4,117 MOHS.
Figure 2.
By paying attention to the condition of your batteries, with awareness of the individual cell/unit inspection values, and maintaining correct saturation, you will maximize their lives and usefulness plus prevent unwanted surprises. Every battery model manufactured has known baseline values that you can reference to as a guide. If you do not know what your values should be, contact me and I will provide that information. With lead-acid batteries there can never be a thermal runaway without the battery first providing many months or years of advance warning.
About the Author
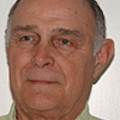