There Were No Underground Damages?
According to the DIRT Annual Report for 2016, damages to telecommunications alone totaled $391 million, and since not all states report through DIRT, we can project that these damage costs are significantly higher.
Let’s ask ourselves hypothetically:
What if we didn’t have any damages to underground facilities?
What if the excavation community had a visual of all underground facilities to avoid damages?
What if locators knew exactly where to mark the facilities?
What if we had a national registry where all facilities were required to provide Global Navigation Satellite System (GNSS) points of underground infrastructure?
What if there was an app that indicated where facilities resided?
What if GNSS and spatial analysis played a role in identifying underground infrastructure?
We don’t believe these questions are too big to tackle, and they should be strongly taken into consideration by everyone involved in planning and constructing underground facilities.
Let’s explore the possibility of having a national registry. For example, what if an Authority Having Jurisdiction (AHJ) took responsibility to own this world? Maybe grants would be available to utility companies to map the existing systems, gathering GPS points, converting existing mapping systems to the necessary Geographic Information System (GIS) data format. For security purposes, there could be a registered number tied to a licensed excavator, facility operator, locate company, etc., to obtain this data, and a possible nominal fee to join, to recover startup costs.
Future Vision?
Consider the electric car, introduced more than 100 years ago. The concept never gained traction because it was a radical idea at that time and the initial costs were far too high. Today, with the American Recovery and Reinvestment Act and Clean Air Act, electric cars are rising in popularity. This is due to what society views is important and innovative. Whether it’s a hybrid, plug-in hybrid, or all-electric, the demand for electric vehicles will continue to climb as prices drop and consumers look for ways to save money at the pump.
Now, consider a parallel example related to excavation equipment. For years, it’s been possible to use GPS and mobile devices to walk a bore-path and create a basic bore plan. GPS connectivity allows you to see your plan and, after the bore, view your As-Built. If this is possible, why are we as contractors, utility companies, and locate companies, not taking advantage of this data? I know some do, but what if we all did? What would be the value of this data to an innovative end user (excavator, city planner, engineer, etc.)?
Would this application require a mandate that utilities provide as-built data of the excavation areas via One Call ticket or via a permit governed by the specific AHJ or utility company? Would these entities provide weekly or monthly Global Navigation Satellite System points of all installed infrastructure? We don’t think so, but how would the data be recorded?
So, what if utility companies wrote a requirement that all contracted locates or future construction projects required a GNSS point every 20 feet of the utility being located or constructed? What if a mobile device captured this data and performed an auto-sync nightly to the utilities main GIS network? Talk about accountability and the value this data could bring to others.
Today, for many organizations there is a tremendous amount of data being lost because information is not captured while our locators or contractors are doing their jobs. What it boils down to is that thousands of man hours every year are spent locating our infrastructure. Yet, once the paint washes off the ground — that data is completely lost.
Technologies are available today to harvest critical underground information, but the investment costs can limit the opportunity to capture that data and store it. As technology evolves, devices to obtain this data are becoming less expensive and far more accurate. One such tool, created by Midco, a cable operator with 380,000
customers across the Midwest, currently tracks all new excavation work (as shown in Figure 1 and Figure 2).
Figure 1. Global Navigation Satellite System web application.
Figure 2. Locator Map — Critical Fiber Buffered Tolerance Zone.
The value of this data has not been fully realized yet. We do know, however, that by tying this data into our locator maps and identifying critical infrastructure we have seen fewer damage incidents.
This is in part due to the volume of data captured during one of Midco’s large-scale projects. This data included structures, utility crossings, depth of infrastructure, depth of utility crossed, GNSS points taken every 20 feet of excavation work, and identified by type of facility placed. For this reason our locate staff can now visibly see on our locator web map that a buffered tolerance zone is identified. This buffer represents a very high valued fiber optic cable and that special considerations and care need to be taken when excavating within this tolerance zone.
What if we have an opportunity to recover some of these dollars by investing in an improved damage prevention system? We need to ask questions within each of our organizations, such as:
• Would the investment in these technologies outweigh the damage costs we incur annually?
• What about the service outage inconveniences to our customers?
• How do these topics affect our company reputation, our customers, and allow us to remain competitive in the markets we serve?
Internally, we asked these very questions as part of a larger customer-focused strategic initiative, and created a damage prevention team of cross-functional employees. In 2016, prior to the team starting their work, Midco experienced 19 severe damages due to varying causes. That all changed in 2017. Since we’ve implemented our best practices, we have experienced only 2 damages; one damage occurred because a locate ticket was not called in, the other damage was caused by large mowing equipment shearing off a fiber pedestal.
If you haven’t guessed by now, our message is about all of us taking accountability and investing in a safer working environment for our employees and communities, which we work in each and every day.
Think about the benefit if these WHAT IFs were already developed, and this data was available for review in a natural disaster situation. Think about these WHAT IFs in a new build situation where locate companies are overwhelmed with the sheer volume of locate tickets. If locates are missed and an app alerts contractors of existing utilities, damages can be averted and drastically reduced/eliminated.
For more information about the DIRT Annual Report for 2016, please visit http://commongroundalliance.com/media-reports/dirt-report-2016.
To download the DIRT Analysis and Recommendations 2016 (PDF), please visit http://commongroundalliance.com/sites/default/files/publications/DIRT%202016%20Annual%20Report_081017_FINAL_Updated_09.20.17.pdf
Look for more WHAT IFs and great discussion at the 3rd Annual Fiber Optic Asset Protection Summit taking place during the CGA 811 Excavation Safety Conference & Expo, March 6-8, 2018, in Phoenix, AZ. Learn more at http://cgaconference.com.
About the Author
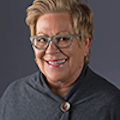