The Changing Role of the Field Technician in the Bandwidth Business
When I started in the telephone business in 1965, the field technician’s jobs were fragmented. Technician’s responsibilities today are even more fragmented. Let’s take a trip from then until now.
THAT WAS THEN
On a new installation it is the responsibility of the dispatch center to program the originating equipment (OE), and to provide wiring information to the central office technician and the installer as to which OE is wired to which horizontal mainframe and to which vertical the feeder cable appears.
• The CO frame technician runs jumper wire from the horizontal main frame to the vertical main frame, and wires the CO equipment to the feeder cable pair.
• The frame technician draws dial tone at the vertical, and dials the automatic number identification to verify that the correct service is on the right cable pair.
• The installer found dial tone on the feeder cable (F1) at the cross box, verify the telephone number, and wire the feeder cable pair to the distribution cable pair (F2).
• The installer then goes to the customer’s workout terminal or pedestal, finds dial tone, verifies the telephone number, and terminates the customer’s drop to the cable pair.
• The installer then installs the network interface, finds dial tone and then pulls in the inside wire, installs the jacks, and then installs the telephones.
InvisiLight® Solution for Deploying Fiber
April 2, 2022Go to Market Faster. Speed up Network Deployment
April 2, 2022Episode 10: Fiber Optic Closure Specs Explained…
April 1, 2022Food for Thought from Our 2022 ICT Visionaries
April 1, 2022When dial tone is present on all phones, the installer dials the quiet line termination and listens. If it sounds good, the technician closes out the install, and moves on to the next install.
If there is any trouble with the initial installation or any existing service, an installation repair technician is dispatched. The installation repair technician is responsible for phones, jacks, inside wire, the service drop, and the distribution cable pair.
• If the problem is on the cable pair, the technician proves the fault into the feeder plant or into the distribution plant.
• If the fault is in the feeder plant, then it is turned over to the cable repair technician.
• If the fault is proved into the distribution plant, then the field technician checks all multiple terminals or pedestals that the cable appeared in. Any terminating faults are repaired, and any cable troubles such as wet cable splices, sheath damage, and circuit design problems, are turned over to the cable maintenance technician.
THE BIG CHANGE
With deregulation, the outside workforce decreases, and the technician’s tasks increases threefold.
• The installer is eliminated, and the installer repair technician takes over initial installations and any repairs.
• The central offices are unmanned.
• The CO technicians are assigned to other departments within the company.
• On a new install, the time-sensitive installer repair technician first goes into the CO, does all of the wirework and all of the paperwork, then goes to the field and finishes the install. Also, any faults found on the cable pair must be identified, found, and fixed.
• Faults on the feeder cable are the responsibility of the cable repair technician.
• Terminating faults on the distribution cable pair are the responsibility of the installation repair technician. Rather than finding a terminating fault in an associated terminal or pedestal that could take hours to find and fix, the technician moves the service to another good distribution pair at the cross box and the customer’s work-out terminal.
This is also the time when FAX machines, caller-ID, answering machines, modems, and burglar alarms, started showing up. This was literally the beginning of bandwidth usage around 300 baud for FAX machines. Baud rates that were maybe 6 to 10 bits increased quickly, jumping from 14.4Kbps-28.8Kbps to 33.6Kbps-56Kbs on substandard cable pairs.
Then DSL hit the market, service went from ADSL to VDSL to VDSL to IPTV and other bandwidth services in a heartbeat. As bandwidth increases, distance from the CO or the remote becomes a problem. End users scream "more bandwidth", and field technicians yell "We don’t guarantee bandwidth on copper cable pairs where you live. If you want more bandwidth, then move closer to town".
There were cable faults that affected both bandwidth service and plain old telephone service (POTS) circuits, such as caller-ID and answering machines. Field technicians use transmission test sets when the cable pair tested OK, but circuit design faults cause complaints of no dial tone, no dial tone at times, bell rings, can’t answer, can’t hear, etc. They measure loop or line current, station ground, circuit loss, circuit, and power influence.
Initially, any failed transmission test is turned over to the ICEP engineer, but with more end-user equipment coming online it forces the field technician to find and fix circuit design faults, making their job more fragmented.
All circuits are affected by unwanted AC voltage on the cable pairs. Field technicians are ill-equipped to find and repair those noise mitigation faults. They are turned over to a quality Inductive Coordination and Electrical Protection (ICEP) engineer, and there are not nearly enough of them. That still holds true today.
If you need noise mitigation help, especially with unwanted AC voltage, you are better off using a contractor who is equipped and has the ability to find and fix those faults. My noise mitigation guru, Russ Gundrum, is one of them. You can contact him at [email protected].
As you can see, the role of the field technician in the bandwidth business is constantly changing. Fiber is rapidly replacing copper for bandwidth. Some field technicians move to the fiber arena; some technicians maintain both the fiber arena and the copper arena. They all need new tools, training, and support.
Like this Article?
Subscribe to ISE magazine and start receiving your FREE monthly copy today!
About the Author
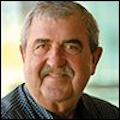