By guest writer Daniel Burch —
The column this month was penned by Dan Burch with Tescom, a company respected for a 35-year history manufacturing quality test equipment targeting the telecom and CATV industry. Dan also has a long history in the industry as a technician and eventually in engineering management. This is a topic dear to my heart. Here’s Dan.
"… Two roads diverged in a wood, and I — I took the one less traveled by, And that has made all the difference." (Robert Frost, The Road Not Taken)
There was once a time in the telephone business (what do we call it now?) that quality ruled supreme and everyone strived for 99.999% reliability. If something broke, it was repaired in a way that would provide years of additional quality service. At some point, the bean counters jumped into the driver’s seat, and productivity became an equal or superior goal. Now the thrust was x number of job tickets per day, with little or no emphasis on quality. Proud, seasoned technicians bucked this new order, with valiant dedication to quality workmanship engrained in them over decades of service to their customers.
First-level supervisors were trapped in a vice, squeezed between a 2nd Liner who demanded results and a seasoned work force who defended the age-old standard of Quality First. To compensate, many managers developed a hit squad of workers who would do whatever it took to sign off 10 or more job tickets each day. This hit squad was needed to offset the lower productivity of those who actually dug up the wet splices, went into the tree line to repair the sheath, and dropped into the manhole to correct the problem. Conversely, the hit squad was a team of cutters, slashers, and rollers, who took every shortcut just to code off a trouble ticket.
During the course of a normal day, technicians encounter a myriad of fault conditions, some of which can be quickly corrected (broken jumper wire, failed drop wire, pair pinched in pedestal lid, etc.). However, many days the remedy involves digging a pit to clean up a wet splice case, opening a sleeve in a manhole to replace a bad connector, or other time-consuming tasks. If a technician is repairing actual faults, their daily productivity should vary every day. Conversely, productivity for the hit squad will be rock solid at a high daily number.
InvisiLight® Solution for Deploying Fiber
April 2, 2022Go to Market Faster. Speed up Network Deployment
April 2, 2022Episode 10: Fiber Optic Closure Specs Explained…
April 1, 2022Food for Thought from Our 2022 ICT Visionaries
April 1, 2022Viewing the activity based on repeated reports is when this practice falls apart. Fast, temporary (dare we say illegal) fixes always lead to other employees returning to fix the actual problem. Within a work group, this causes friction and resentment when good workers have to follow-up on and make right the dastardly mess created by the cheaters. Adding salt to the wound, managers praised the "fast turnover" teams, admonishing the rest to follow their excellent example.
So, two roads diverged in the woods; one to cheat and repair nothing, and the other, less traveled, that repairs every fault the first trip. I took the one less traveled by.
However, there is no short-term glory in doing it right. In many shops (though not all, I’m told), you may be ridiculed by your peers and chastised by your boss.
However, I took the one less traveled by, and that made all the difference. My productivity was up and down any given day, depending on the fault encountered, but with a single splice pit we avoided 100 more trouble tickets. In the end, I entered Engineering & Management, and they all worked for me. The hit squad fled.
Lee Iacocca said Quality and quantity are on the same side of the coin, and that still holds true today. For all those who took the road less traveled by, you have the satisfaction that you performed your duties at the best of your ability, and the customer is the winner. At the end of our journey you have the satisfaction of having done it right. And that makes all the difference.
In the years since I originally penned this note, we have achieved a partial level of transition to fiber in the Last Mile. However, we still meet managers who say their hands are tied on properly maintaining the remaining copper plant. The premise was that all copper would have been replaced by fiber by now. However, until the last customer on the last piece of copper is migrated to fiber or wireless, the plant must provide some acceptable level of service. Due to years of deferred maintenance, much copper plant today is in high-maintenance mode, and companies lack the funds to transition all customers to fiber and wireless. This transition is perhaps still a decade away if it is ever achieved entirely. Until then, companies still need some of their employees to "take the road less traveled by…."
About the Author
Daniel Burch, TesCom USA, can be reached by email [email protected], or for more information, please visit https://tescomusa.com/.
Like this Article?
Subscribe to ISE magazine and start receiving your FREE monthly copy today!
Signing off
Thank you, Dan. Sometimes I feel like the strict dad who keeps enforcing old-time values and rules. It’s nice to hear this story come from other highly qualified and talented folks like you. I realize that dealing with budgets, with the focus on fiber makes it difficult to give time and attention to copper cable, but copper is still going to be around for a long time. Moving out of copper is complex, and fraught with political and budget issues, so meanwhile, treat it well — and your customers will thank you. You can reach me at [email protected] or text or call me at 831.818.3930.
About the Author
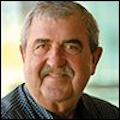