Be Diligent About Your Optical Fiber Selections —
There are cables designed for every environment. One might argue there are too many options and that deciding between designs is not simple. Choosing a cable not only requires fiber type and count, but also confirming that the cable will last for the expected lifetime of the application.
Cables need to resist mechanical and environmental stresses both during the installation and where the cable is finally placed. Since installation is a significant portion of the overall cost of a cabling system, selecting the right cable mitigates expensive replacement costs.
InvisiLight® Solution for Deploying Fiber
April 2, 2022Go to Market Faster. Speed up Network Deployment
April 2, 2022Episode 10: Fiber Optic Closure Specs Explained…
April 1, 2022Food for Thought from Our 2022 ICT Visionaries
April 1, 2022Consult Industry Standards
From the beginning of a project, specifying the correct industry cable standard is critical to ensure that the cable performance meets the demand of the application. Standards address the majority of use cases, but in certain environments additional requirements for performance and safety may be necessary. In most situations, it’s important to also share the details of your application with the cable manufacturer so they understand the final installed application.
There is a hierarchy in standards depending on what you are specifying. Each tier describes what is necessary for the successful implementation of that network layer. For example, if you are installing a passive optical network in a campus environment, the applicable standards would be, in order, as follows:
1. IEEE 802.3ah, 802.3av (EPON) or ITU G.984, G.987, G.989 (GPON) specify the networking protocol and channel performance. These specifications are constantly evolving to address higher transmission speeds, so this list is not all-inclusive.
2. ANSI/TIA-758 extracts the physical media requirements of IEEE and ITU and translates them into cable and connectivity requirements. TIA documents typically reference the appropriate ICEA specifications to attain the necessary physical requirements for the cabling system.
3. ICEA S-87-640-2016 (OSP), ICEA S-104-696-2019 (Indoor/Outdoor), and other ICEA documents specify the physical, mechanical, and environmental, requirements the cables must pass using ANSI/TIA-455 (FOTP) test methods.
4. BICSI-G1-DL-17 completes the list with recommended general practices for OSP construction and installation.
It is important to familiarize yourself with the last 2 tiers since they impact the cable characteristics, where it can be installed, and the best installation practices.
Protecting the Optical Fibers
Optical fiber cables are designed to protect the inner fibers from external stresses. Excessive external mechanical stresses can increase optical attenuation, and reduce the usable life span of the fibers.
Cables can experience tensile forces during and after installation. Strength elements such as aramid or fiberglass-reinforced polymer (FRP) yarns and rigid steel or glass-reinforced plastic (GRP) components give the cable the necessary properties to mitigate these stresses. Longitudinal compressive forces due to low temperatures can be counteracted only by rigid strength elements.
Figure 1. Fiber sub-units in a helical wrap.
To alleviate stress on the optical fibers within the outer sheath of the cable, fiber subunits are often laid in a helical fashion, like a telephone handset cord. (See Figure 1.) This allows the cable to expand and contract during installation in varying weather conditions without damaging the fibers. To facilitate mid-entry to a cable, most manufacturers reverse direction of the helix approximately every 6 feet.
Polyethylene, whether medium- or high-density, offers great moisture resistance and very low temperature brittleness, typically to around -100°C, and is the material of choice for OSP cable jackets. To survive long-term exposure to UV radiation in sunlight, carbon black is added to the compound. Other chemical UV stabilizers are typically added, but carbon black is ideal since it prevents UV induced oxidation. Yellow- or orange-jacketed cables do not have the longevity of a cable that uses carbon black.
Figure 2. Armored cable with corrugated steel tape.
Aside from necessary tensile and bend radius properties, cables must be able to withstand compression, especially if the cable is direct buried. For best practices when direct burying a cable, the cable should be armored using continuous corrugated steel tape (CCST) to prevent point compression due to rocks. (See Figure 2.) Aluminum interlock armored cables are not recommended for direct buried installations.
For rodent protection, CCST is regarded as the best option. Although there are non-metallic options available, including nylon jackets, glass yarns, and chemical repellents, metallic armor remains the most reliable.
In applications with a high water table or where flooding is likely, the choice of water-blocking solution is critical. Since brackish and seawater have high ionic strengths, only gel-filled cables are suitable. In freshwater applications, it is possible to specify dry-block or super-absorbent-powder (SAP) type cable.
Indoor / Outdoor Cables
A standard OSP jacketed cable is permitted only 50 feet into a structure, unless it is in a conduit. Having an indoor/outdoor (I/O) cable alleviates the need for a transition point between OSP and inside plant (ISP) cables. The I/O cable must have the necessary fire safety ratings, typically riser (OFNR) or plenum (OFNP). While millions of feet of both riser and plenum versions have been installed without incidence, there have been issues.
For riser cables, the PVC compound used for the jacket material is highly plasticized to make it flexible and easier to install. Fungus present in soil will consume any plasticizer at the surface, leading to more plasticizer migration. The net effect of this is that the jacket becomes brittle and can cause attenuation at temperatures above the cable’s rated low temperature limit.
For plenum cables, the situation is different. Plenum cables are required to pass NFPA 262, which has both peak and average smoke requirements. For the cable to pass NFPA 262, smoke suppressants are added to the PVC. Unfortunately, if a cable is submerged in water for extended periods, the water can migrate through the jacket material, taking the smoke suppressant with it. Despite the presence of dry water-block, the moisture may eventually migrate to the end of the cable at the splice enclosure and evaporate, leaving behind smoke suppressant. Enough suppressant can accumulate to cause attenuation of the fibers in the enclosure. There is an alternative jacketing material that doesn’t have this issue: PVDF.
PVDF (a chloro-fluoropolymer) is a material that has been used for years as an architectural coating, helping to preserve the exterior of commercial buildings. It is resistant to chemicals, heat, moisture, and UV light, allowing end users to procure cables in any color without concern for sunlight UV degradation. While more expensive than PVC, overall it is still less expensive than replacing a plenum PVC cable.
Unforeseen Encounters
Even with the best planned routes, unforeseen obstacles can delay or even prevent cables from being installed. Those who have installed in urban areas are familiar with finding other utilities or services that are not where the maps indicated. In rural or wide open areas, rock outcroppings, underground springs, streams, or swamps, can be encountered.
Even steam, which you might think would be the purview of urban or campus locations, has been seen in the wild. In 1991, Williams Communications was installing standard OSP cable in decommissioned pipelines just north of Bakersfield in an area where steam was being injected under high pressure to help recover shale oil. The cable in that pipeline began showing high attenuation and after reaching the underground cement splice vault, it was discovered that escaping steam had melted the cable. Only the steel central strength element and the optical fibers remained. The original cable had to be replaced with a temperature- and steam-resistant Steampeth cable.
Like this Article?
Subscribe to ISE magazine and start receiving your FREE monthly copy today!
Final Thoughts
There are other environmental and mechanical stresses that were not discussed in this article, but by using the standards and working with the cable manufacturer, the best choice of cable can be made.
Keep in mind a few questions when starting a project:
• What is the expected temperature range?
• Will the cable be exposed to sunlight?
• For aerial cables, what are the wind and/or ice loading conditions that will affect span length?
• For direct buried cables, what are the mechanical forces due to soil type?
• For all buried cables, what is the impact of water table levels or the propensity to flooding?
• For cables transitioning from the outside plant into the premises, what fire safety requirements need to be considered?
Asking the right questions beforehand can ensure a smooth installation and save on expensive replacement costs.
About the Author
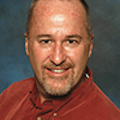