It Can Come True When You Make the Right Play —
"Time is money." A familiar statement on which we can all agree, yet even more so for network operators with robust plans to deploy fiber. Up to 70% of the total cost to build an FTTx network is labor, with time spent on tasks such as fiber placement, splicing, and other construction-related tasks. Traditional old-school splicing requires expensive equipment and a skilled technician needed to do the job and test the work once done. All with the clock ticking to get customers up and running.
And what about the other factors that shape FTTx deployments? While it is tempting to save money up front by picking a lower cost terminal, the true cost per installation requires both hardware and labor installation. In addition, things break all the time (e.g., cars hit utility poles, lightning strikes short out connections), and you can never underestimate the power of a random backhoe to ruin a day. Ease of repair in the field must be a major consideration. Again, time is money.
By taking a second look at factory-installed, pre-connectorized cable, network designers and contractors can use a modular and flexible design methodology that scales across the application environment. This approach will ensure rapid installation, and savings of time and money today and into the future.
How is this possible?
No More of Your Daddy’s Drops
You may have considered using plug-and-play solutions in the past, but slack storage, the need to manage extra stock of various drop cable lengths, tight design requirements, and excessive material costs, were just some of the myriad of concerns that may have stopped you from taking the leap.
Many FTTx drop solutions were originally designed for the large Regional Bell Operating Companies (RBOCs) when they were first deploying their networks, which required use of flat drop cables and at least one splice to install a drop from the pedestal to the home. A large, flat drop cable makes it difficult to store excess cable in a small footprint. In most cases, the provider would buy the drop cable as a pigtail (connectorized on one end and stub on the other). The terminated end would be installed into a weatherproof terminal at the curb, and the blunt end would be cut to length and fusion-spliced to a short pigtail stub and installed into the ONT. While this solution has been deployed very broadly, it has some inherent issues.
The main issues include:
• The need for a trained fusion-splicing tech and spicing equipment.
• Slows down deployment times vs. a fully plug-and-play design.
• If the drop cable is cut, a splicer will be required for restoration.
• Many different lengths must be inventoried to prepare for each drop scenario.
Drop solutions have come a long way in the last several years. If you default to your current method because "we’ve always done it that way," it may be time to look at pre-connectorized drops to get the job done.
The Better Way to Drop
Getting to FTTx utopia thrives on pre-connectorized, plug-and-play solutions. (See Figure 1.)
Figure 1. This terminal is designed to accept any drop cable media.
Due to the high variability of FTTx architectures, extensive engineering has been required to ensure proper cable lengths for deployments. Today, pre-connectorized drops come in many different varieties to best suit the environment and build priorities.
Utilizing the small form factor of fiber has also allowed a pre-connectorized drop and any fiber slack to be mounted at the destination site. There, the desired length is simply pulled from a deploy wheel to the access point. Once the pullable connector has reached its destination, the connector assembly is completed with the supplied connector housings and the connector is mated to the adapter. The remaining slack is pre-stored with no further slack management required, removing the slack storage obstacle.
A plug-and-play approach to pre-terminated fiber that is factory-tested and certified reduces on-site labor by eliminating or significantly reducing the need for field splicing with its associated time and overhead. Think about it like this: without the need for extensive training, and by minimizing splicing at the drop, service providers and network planners can rely on minimally skilled labor to speed fiber rollouts as opposed to a fully spliced drop network. This allows highly-skilled splicing technicians to be where they are needed — installing high-count fibers required in the core of the network — so that less of their time (and money) is spent adding fiber drops and connecting customers.
Dirt, dust, and humidity also come into play during field work splicing, which also must be properly tested before being put into service. With plug-and-play, installers simply pull fiber, inspect, and clean connectors, and plug them in at the pedestal and at the customer end. This process requires no equipment setup, no skilled technician for splicing, and no fretting about environmental conditions playing havoc with splice quality. Tool-less installation means quick service turn-up, which translates to adding more customers and revenue faster.
By taking a fiber delivery platform that allows you to use multiple drop types designed for all environments, network providers will experience fewer headaches by needing fewer SKUs in inventory. This removes the need to buy a different drop terminal solution when network requirements change, and with all training and support overhead that comes along with it.
An ideal modular drop terminal system design should be configured to support multiple network options out of the box while supporting any industry drop cable option, including flat drop, cable-in-conduit, and 10 mm microduct. Finally, the terminal should be equally at home installed on a pole, in a pedestal, or below ground, with only a superficial change needed for the appropriate attachment hardware. (See Figure 2.)
Figure 2. Our terminal, improving the application and craft experience.
Once service is established, the benefits of a pre-connectorized, plug-and-play approach provides a boon in time savings for troubleshooting and repair. Connectors, fiber, and customized components, are designed to be craft-friendly, allowing a technician to quickly and easily test and repair all items in a bad connection, instead of a "rip and replace" field job to repair the cut fiber, remove the old hardware, install new hardware, and finally re-splice the fiber to restore service. Downtime and installation time for a network change is minimized, freeing up technicians to move onto the next job.
The plug-and-play modularity afforded by a pre-connectorized fiber cable also has one other significant benefit. Using modular, snap-in hardware means when network changes are needed as service expands and requirements evolve, it’s easy to go back to a modular terminal out in the field and simply reconfigure it for a new task by swapping in different components and/or cartridges to gain the functionality necessary. A plug-and-play approach to FTTx deployments provides a future-proof path for network gear by providing flexibility for reconfiguration in the field as needs change, providing more savings in time and money.
A modular solution such as the Clearfield YOURx-Terminal can be reconfigured to support a straight drop terminal application, drop and express terminal, and a splitter terminal when needed. Engineers need to do a bit of upfront planning to determine the drop cable lengths, which in turn determines the number and positions of terminals needed. Some micro cables store beautifully at the customer premises, but they can reach only up to 300 feet. Beyond that distance, choosing a different type of drop cable is required.
Investing in Your Future
When designing your next FTTx development, please keep in mind that many of the challenges associated with a plug-and-play solution in the past no longer have to be an issue. Gone are the days of a provider needing to store excessive drop cable lengths on the inventory shelf. Also, the need for large amounts of slack storage has been alleviated by using smaller signature cable and duct systems.
While investing in pre-connectorized fiber and a modular terminal solution isn’t a magic bullet for fiber deployments, whether you are paying a contractor or doing your own splicing, it’s important to reevaluate the OpEx and CapEx cost savings of a pre-connectorized drop solution with this alternative approach. It’s a combination guaranteed and proven to save time and money, moving that much closer to a utopian FTTx network deployment.
Save
Save
About the Author
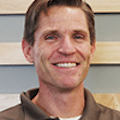