Flexibility: The Key to FTTX Success
Bend. Don’t break. This timeless advice may have originated in ancient China, but is still relevant today given the many challenges facing service providers and equipment manufacturers. It certainly resonates to service providers trying to complete fiber network build-outs in a time of supply chain disruptions, material shortages, and labor scarcity.
Rather than allowing these troublesome developments to break their fiber project schedules, providers are learning to be flexible in their infrastructure choices and methods. Additionally, service providers are adapting their operational procedures to keep their FTTX build-outs on track and adapting their network architecture to correspond with the equipment that is available in the current market. Savvy service providers are adapting by embracing alternative ways to achieve their project objectives when the old ways are no longer viable.
"Collaboration between providers and manufacturers is the key to success as the challenges that face both require flexibility, ingenuity, and the tenacity to overcome and succeed despite the current supply chain climate."
Service providers aren’t the only ones facing challenges in recent years. Communication equipment manufacturers are also experiencing a dramatic shift in operations. The COVID-19 pandemic and global conflicts have negatively impacted raw material availability and skilled workforce labor. Product lead times have gone from weeks, to months, to years, in some cases. Raw material availability has plummeted while prices have skyrocketed for many commodity components vital to equipment production; including steel, aluminum, plastic resins, paints, coatings, and additives. Manufacturers often cannot procure the materials they need in a timely fashion to keep manufacturing lines producing without delay. Considering these challenges, progressive manufacturers are introducing new options to their product lines that take advantage of more readily available materials and increased production efficiency.
Equipment manufacturers are working with providers to adapt to this unpredictable environment. Service providers continue to operate “full speed ahead” as RDOF and other federally funded broadband programs have fueled thousands of new fiber projects throughout the US.
Yet the pace of these projects is being restricted by infrastructure availability. When the fiber optic distribution hardware and the environmental enclosures that house them aren’t in stock or readily available, project schedules can be threatened or delayed. To ease their customers’ burdens, some equipment manufacturers are taking the lead by educating providers about alternative ways to achieve their FTTX objectives and providing hardware options to accomplish those goals. Collaboration between providers and manufacturers is the key to success as the challenges that face both require flexibility, ingenuity, and the tenacity to overcome and succeed despite the current supply chain climate.
One way equipment manufacturers are helping providers is by offering alternative form factors for equipment that performs similar network tasks. For instance, fiber distribution hubs are manufactured as pedestal, metal cabinets, or compact, pole mount terminals. If a service provider is flexible in the way they approach their fiber hub strategy, having three different style hubs available to them can often alleviate project delays if their preferred form factor has longer lead times than another type. For instance, if PVC is in short supply at the moment, a provider may find that a metal cabinet or terminal type fiber hub will have greater availability and a shorter lead time than a pedestal type hub. (See Figure 1.)
Exploring form factor options with their equipment manufacturer partners can lead to unexpected discoveries for new FTTX OSP options. In residential areas where fiber distribution points dot the landscape, those points can also take on a variety of form factors. Providers may find below-grade enclosures/buried vaults or pole mount terminals that meet their fiber aggregation and demarcation requirements just as well as buried distribution pedestals. These various form factors give providers more opportunities for deployment in times of limited product availability.
Flexibility in splicing methods and the type of fiber optic cable chosen is another way providers can increase the number of distribution enclosure options available to them. A provider that utilizes loose tube fiber exclusively may find their choices of environmental enclosures that support this type of fiber more limited than a provider that is open to using ribbon fiber in their network as well. In addition, using preconnectorized stubs can also reduce deployment time by removing the splicing that would otherwise be done in the terminal. All three are viable options for FTTX distribution, so a provider open to using multiple fiber types has more options available to them for distribution pedestals, below-grade enclosures, and wall or pole mount cabinets to protect those splice points.
One final consideration for service providers and engineering firms that find they are facing product unavailability or long lead times is to talk directly with their equipment providers. Manufacturers want to help their customers succeed. If they can’t provide a solution to their customers’ FTTX equipment needs due to raw material or component shortages, they may be able to work with the provider to develop new product configurations or alternative product designs that meet the project's requirements and can be produced using more readily available materials.
Undoubtedly, the current business environment, with its labor and supply chain issues, is a challenge for both equipment manufacturers and service providers to navigate. Every day seems to bring new obstacles for sourcing managers and network planners to overcome. Remaining flexible about network design, equipment alternatives, and fiber type can help remove some of those obstacles by exploring alternatives that can shorten lead times while meeting all project objectives. It’s a “bend, don’t break” mindset that can keep your FTTX projects moving forward.
ABOUT THE AUTHORS
Kelly Henry and Rick Koca are Senior Product Managers with Charles Industries, LLC, managing fiber pedestal, terminal, hub, and below-grade solutions designed for rapid FTTX deployment. For more information, please visit www.charlesindustries.com. Follow them on LinkedIn: charles-industries and Facebook: charlesind.
About the Author
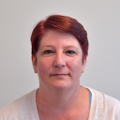
Kelly Henry
Kelly Henry is a Senior Product Manager with Charles Industries, LLC, managing fiber pedestal, terminal, hub, and below-grade solutions designed for rapid FTTX deployment. For more information, please visit www.charlesindustries.com. Follow them on LinkedIn: charles-industries and Facebook: charlesind.
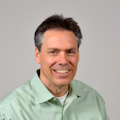
Rick Koca
Rick Koca is a Senior Product Manager with Charles Industries, LLC, managing fiber pedestal, terminal, hub, and below-grade solutions designed for rapid FTTX deployment. For more information, please visit www.charlesindustries.com. Follow them on LinkedIn: charles-industries and Facebook: charlesind.