Hiring and Managing Fiber Contractors for a Successful Project —
This is Part 1 of a 2-part series that looks at establishing and cultivating good working relationships with contractors for fiber optic communications projects. This article focuses on contractor selection and
maintaining good communications. (Part 2 will review expertise gaps and training strategies when working
with contractors.)
All communications networks experience a life cycle. They are planned, designed, procured, installed, provisioned, and maintained. Throughout their life they experience degradation, technology changes, and, likely, equipment/technology obsolescence. Due to these changes and others required by market forces, the cycle must sometimes be repeated from its beginning.
While networks can be "living things" with constant provisioning and rearrangements, the installation of new network infrastructure is a process that occurs only once every number of years, or even decades. It doesn’t make sense for a telecommunications operator to keep staff on hand to rebuild the network infrastructure, so when these projects occur they are largely accomplished by contractors.
Installation Goals / Selecting Contractors
Normally, the operator or service provider has a few major goals for their network infrastructure build. It must:
• Meet performance goals — through adherence to design.
• Exhibit high reliability — through quality construction.
• Be cost-effective — through productivity and efficiency.
Principals should be available to answer questions and clarify any confusion regarding network design and performance specifications.
A successful project will start with a well-defined, detailed design that must be clearly communicated to the contractors and the staff reviewing the bid proposals. Quality construction requires that the installers have the right tools, knowledge, and skills, to properly implement the design. Quality is also enhanced by regular communications with the contractors during the project regarding any noted deficiencies that require rework or adjustments. Productivity and efficiency will be achieved through highly skilled technicians who work efficiently, and the effective management of resources during project execution.
Before submitting a Request for Proposal (RFP) to a number of contractors, it makes sense to limit the pool of contractors under consideration to those most likely to successfully implement the project. A Request for Information (RFI) can serve this purpose by soliciting the qualifications of the candidates.
Reasonable business questions may request detailed information on:
SIZE AND CAPACITY
• How many qualified technicians of a given type are employed by the contractor?
• Splicers?
• Testers?
• How many fusion splicers, OTDRs, power meters, connector endface inspection probes are on hand?
• How many cable winches or directional boring units are on hand, or will be employed?
• How many kilometers of fiber cable of a given type can the contractor bore, bury, plow, hang per day?
CAPABILITY
• What types of fusion splicers are owned?
• Single fiber or multi-fiber ribbon?
• Fixed V-groove or profile alignment?
EXPERTISE
• What reference projects can the contractor document as having completed?
• What training, expertise, and/or certifications does the contractor and their personnel possess?
• Are their knowledge and skills current?
Note that each question has a direct bearing on the contractor’s likelihood of success on the project. For example, a contractor with only fixed V-groove splicers may be fine for a Fiber-to-the-Home project but will be unlikely to achieve the specified splice losses for an ultra-low-loss long-haul project.
InvisiLight® Solution for Deploying Fiber
April 2, 2022Go to Market Faster. Speed up Network Deployment
April 2, 2022Episode 10: Fiber Optic Closure Specs Explained…
April 1, 2022Food for Thought from Our 2022 ICT Visionaries
April 1, 2022Communicating With Contractors: The Planning Phase
The purpose of early communication with contractors is to detail the specific project design to them, largely through a Statement of Work (SOW). The SOW must be in-depth and unambiguous to ensure the contractor’s ability to properly implement the original design. A contractor cannot adhere to a design that is not well-defined.
• Callouts of construction details in drawings are very useful. Actual sample mockups or photos of splice closure buffer tube/ribbon routing and dressing takes a few hours to build but allows no room to misunderstand expectations.
• Citation of industry standards can be helpful, but many standards are written to allow for multiple options or performance levels.
• Anything that can be misunderstood or interpreted in several ways must be defined.
The SOW should also specify the deliverable performance data on the properly-constructed and commissioned fiber system. These test results confirm the quality of the system, and can be as detailed as the principal requires. The service provider, however, should define a single format for all results from all subcontractors to avoid a burdensome data conversion task.
Service providers may also wish to hire additional temporary engineering staff to review, accept, and/or audit, if a high volume of data is expected. If a project is large enough that the operating company cannot build it without outside help, it’s also a very strong possibility that the company will not have adequate organic staff to properly audit the commissioning data. Rapid review of this data is essential to project productivity and to highlight concerns early in the project when they can be more easily addressed.
Communicating With Contractors: The Execution Phase
During the execution phase, proper two-way communication between the contractor and the service provider can ensure adherence to design, quality, and productivity.
Early on, you should commit to high availability to the contractors in the field to answer any questions or clarify any confusion regarding the network design and performance specifications. This may put a temporary burden on your personnel, but it is critical that you allocate additional staff to perform this task. If any deficiencies are detected in the clarity of the SOW, an engineering change should be issued immediately to all subcontractors — not only to the contractor who first noted the deficiency.
As a project progresses, you should be spot checking the quality of each subcontractor’s work and, ideally, each individual crew working for the contractor. Discrepancies and required rework should be noted immediately; if discrepancies are repetitive, the crews with inadequate expertise should be flagged. Remedial actions in these cases should be pre-defined in the terms of the contract (i.e., requiring the contractor, or allowing you, to place additional supervision on the subject crew for a defined period of time).
Note that communication must be two-way. Text messaging may not be sufficient; the text that is never read may as well never have been sent. Take the time to pick up the telephone and talk to someone!
The other purpose of communication is to ensure productivity and efficiency through logistics management. This usually means the coordination of resources between the service provider, the contractor, and third parties (i.e., traffic control (automotive) resources, building access, definition or creation of maintenance windows (rolling traffic off circuits to be worked on, etc.) It may also mean approving work subunits and executing timely partial payments to contractors.
Like this Article?
Subscribe to ISE magazine and start receiving your FREE monthly copy today!
Conclusions
Proper management of contractors starts with proper selection of contractors. Proper communications with contractors begin with a well-documented design and clear communication of that design.
Frequent two-way communication and feedback is required throughout the project. The increased volume of communication, documentation, and supervision, required during execution may necessitate that the service provider reallocate or even hire additional personnel to perform these tasks.
Consideration and attention to these issues should go a long way in achieving the stated goals of adhering to the design, maximizing productivity, and ensuring quality construction.
Nonetheless, any deficiency in the skills and knowledge required to successfully implement the project, be it you or the contractor, may still preclude a successful outcome. Identifying and eliminating these gaps in expertise and training strategies for principals and contractors will be covered in Part 2 of this series.
About the Author
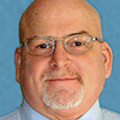